Historically, the Cooling Tower fans and Industrial Air Coolers lack a performance monitoring and control, by design, and when they start operating they are submitted to maintenance and inspection plans falling behind the importance of those in relation to the industrial production.
Figures 1 and 2 show typical Cooling Tower and Air Cooler arrangements.

Figure 1 - Industrial Cooling Tower, image by FanTR (2020)

Figure 2 - Industrial Air Cooler, image provided by client (2011)
The consequence of this context is the occurrence of failure in the equipment, with extension of damage caused to other components associated to the functioning of: transmission axis, couplings, occasionally the reducer and the electric engine in Cooling Towers and activation sets, axis and bearings in Air Coolers. Additionally, consider the associated production losses or the risk of it.
The purpose of this article is to signal to the Maintenance, Reliability and Operation Engineering professionals responsible for that equipment of the need to include inspection and intervention actions in the maintenance plans, as well as to implement monitoring and control instrumentation. Those actions help to maintain the Industrial Unit production program, aiming to reduce failures in the equipment and adjusting it to the operational conditions.
The Fan, its typical structure and work environment
The Cooling Tower and Air Cooler Fan are simple to build, with few components, as shown in Figure 3.

Figure 3 - Image of a typical fan, image by FanTR (2024)
The FanTR Fan Rotor is made of the following components:
- Central cube
- Lower disks and upper ring;
- Studs, comprised of machine screws or stud bolts, nuts and flat washers.
- Two-part bearing, in aluminum or stainless steel;
- Blade, in fiber glass material, coated in stainless steel tape on the leading edge.
They operate continuously in operational campaigns which can vary from 01 to 04 years and are subject to aggressive environmental conditions, in the case of Cooling Towers and high temperatures, in the case of Air Coolers.
During that period, the Reliability of each component must be sufficient as to not allow the occurrence of failures.
The occurrence of failures and critical components
Throughout years overseeing assemblies, maintenance, inspections and failure analyses, we observed that some components of the fan are more critical than others, in terms of failure.
With regard to the Cooling Tower fans, the studs (bolts, double end threaded studs, nuts and washers) are those with the shortest Mean Time Between Failures (MTBF). They are components which work under the regime of cyclical effort and under severe corrosion conditions, allowing a failure by fatigue, due to the corrosion.
Images in Figure 4 and 5 show situations of the studs in which there was a failure, or which were about to fail:

Figure 4: Failure in the operation of the blade two-part bearing set screw, by Failure Analysis Report (2017)
In the case of Figure 2, in the failure assessed, it was shown that the fan had been operating for almost 05 years without any inspection activity.

Figure 5: bolts in state of advanced corrosion in operation, image provided by client (2019)
Figure 5 shows the heads of bolts completely “coated” by the corrosion attack of the Tower product. We identified that they went through two 2-year operational campaigns without being replaced.
In Air Coolers, the factor which accelerates the occurrence of failures is the temperature of the coils, finned tubes, through which the heated product passes. Studs are the elements which present the most failures.
Due to the change of the operational procedure issue, disrupting the equipment, whether it be due to maintenance or inspection, the fans are stopped without removing the heated product from circulation, creating an increase in the temperature of the VT plan, dilating the bolts and reducing the initial tightness of the blades, whose lack moves toward the circular Air Cooler wall once they resume operation, stopping the whole rotor. Figure 6 shows the blade stopped against the circular wall, referring to an Air Cooler in the situation described above.

Figure 6: Blade against the Air Cooler wall, image provided by cliente (2015)
In old Air Coolers with aluminum blades, a typical fatigue failure type was identified. This failure is shown in Figure 7.

Figure 7 – crack in aluminum blade neck, image provided by client (2014)
Still with regard to Cooling Tower Fans, the blade is another component which can present excessive wear due to abnormal operation conditions. The excess of drops dragging, caused by failure in the padding and the mist eliminators, accelerate the wear on the leading and trailing edges.
The other components, central cube, lower disk, upper rings and two-part bearings have a longer useful life, requiring inspection only in programmed interventions.
Recommendation on the level of Reliability
On the level of Reliability, it is desired that the Cooling Tower or Air Cooler fan does not fail on the period of the campaign, affecting the production program and increasing the costs of maintenance.
For that purpose, the database for the registration of inspection and maintenance is the base to establish the frequency and scope of the intervention.
If such database does not exist, inspections must mandatorily be made between campaigns or programmed or general stops in the critical components, such as studs, blade, bearings, belts and pulleys to assess the level of wear of each component and, with that, define the new frequency of inspection / intervention.
Suggestion of the Inspection and Maintenance Plan
The recommendations for the maintenance team for those fans are listed below on Table 1.
In Cooling Tower fans, we recommend:

Table 1 - Inspection/maintenance recommendations - VT Cooling Towers
In Air Cooler fans, we recommend:
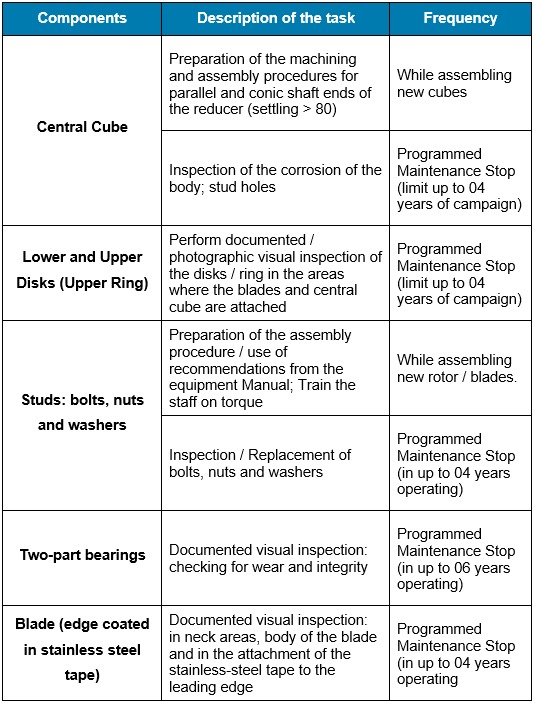

Table 2 - inspection/maintenance recommendations - VT Air Coolers
Suggestions for Improvement
In the beginning of this Article, we mentioned that many installations of the Cooling Tower fans and Air Coolers lacked a monitoring of conditions and control systems. In Cooling Towers with transmission axis between the reducer and the electric engine, some organizations adopted the routine of reading the vibration of the electric engine, obtaining signals which do not allow a good diagnosis of that is happening inside the cell, fan and reducer.
In other facilities, the maintenance and reliability engineering has implemented:
- Modernization of old fans, replacing equipment by advanced aerodynamic projects which allow operations with better performance due to the smaller consumption of power by the electric engine, increase in air flow rate, reduction of noise, in addition to being lighter than the previous ones and being easier to assemble and disassemble (better maintainability).
- Vibration sensors on the inflow and outflow axes of the reducer, with storing capacity of the vibration signals in the 03 directions, vertical, horizontal and axial, and the surface temperature of the spot installed. Those sensors are able to transmit that data via Bluetooth from a certain distance from the pickup, be it a cellphone, a tablet etc...
- Frequency inverter in one of the fans, to allow a modulation of the use of the fan due to the thermal exchange of the Tower; The IF is commanded by PLC, which receives a signal from the transmitter of the temperature of the water leaving the Tower and returning to the industrial plant (cool water).
Final Considerations
Throughout the last few years, the Cooling Towers and Air Cooler got more attention in Maintenance and Reliability Engineering. The Maintenance and Inspection Plans became more adequate to the function of the equipment in their industrial facilities.
Modernization has been adopted by many industries, promoting the replacement of fans by equipment with better aerodynamic profile and higher operational performance.
Along with the revision of the Inspection Plans, devices to monitor the conditions and a control system were included to obtain a better adaptation of the equipment to the operational condition.
The result measured by some organizations was to operate whole campaigns without the fans failing. In addition to obtaining gains in consumption of power and ventilation in the Cooling Tower and Air Coolers.
By Emerson Carlos Assunção Sanches
Mechanical engineer, MSc in Mechatronics by UFBa, having been acting in Maintenance of Rotating Equipment since 1978 and in Reliability since 2009. Training courses in Reliability Engineering at Reliasoft / Compass. Works of Cementing, Ferrous Metallurgy and Petrochemical industries applied in the facilities. Currently a professor of the Undergraduate and Graduate programs at Cimatec, in the subject of Reliability. Email: eng_spec@terra.com.br